|
|
|
|
Surface Structure
Fig 1 (Replicated SEM Picture 1 Pickled plate)
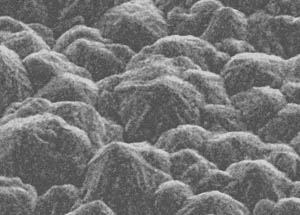
|
|
|
Metals are crystalline structures with relatively large grain boundaries and thus when looking closely as such surfaces these should be evident. Mechanically manipulated surfaces do not allow us to see the surface clearly and entrap multiple contaminants out of sight. Even when looking closely at raw mill pickled plate, it is easy to see the crystalline structure Fig 1. |
|
|
Fig 2 (Replicated SEM Picture 2 400 grit surface)
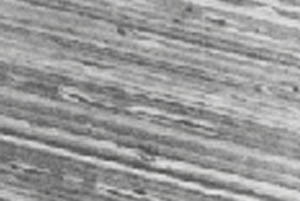 |
|
|
When the surfaces are mechanical treated to the desired level, whether that be 120, 240, 380, 400, 600 grit or mirror polished with mops they do not expose the true material and often have undesirable inclusions and contaminants. Fig 2 shows a 400 grit mechanically treated surface under 650 x magnification. This surface already is in abundance with contaminants and a perfect site for pyrogens (Germs) to grow. The roughness, especially the micro attracts the adhesion of small molecules. In service the surface would allow contaminants and substances to build, fester and create local entrapments growing exponentially to levels that affect the overall performance of the end product whether it be a surgical implant, polymer reactor, heat exchanger, or liquid / gas conveyance lines. |
|
|
Fig 3 (Replicated SEM Picture 3 mirror polished surface)
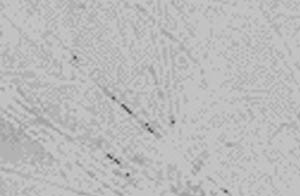
|
|
|
When the surface is taken all the steps to a full mirror polish, the surface is perceived to be clean. On close examination, the surface does not show its natural crystalline structure and in fact shows a contaminant that has been dragged in by the mechnical mop. |
|
|
Fig 4 (Replicated SEM Picture 4 Electropolished surface from 400 grit)
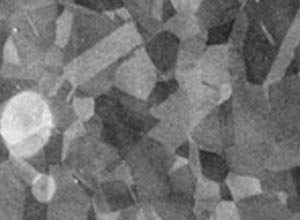
|
|
|
When the surface as shown in Fig 2 has been optimised by the electropolishing process a full crystalline structure is apparent. The upper damaged layers of material have been removed and lower undisturbed layers exposed. The material can now perform to its full potential, leading to a trouble free, low maintain service life of whatever component the original material has been specified for. |
|
|
|
|
|
Deburring & Edge Rounding
The electropolishing process is also used for deburring, where mechanical means, especially when dealing with fine burrs, do not fully remove the burr by flapping it over one side or the other. As the process dissolves the peaks in preference the burrs are removed easily, creating desirable rounded smooth edges.
|
|
|
Edge & Point Shaping
In some applications, edges and tips of points (typically needles) require shaping. Under careful control of the parameters these profiles can often be shaped within a desired envelope.
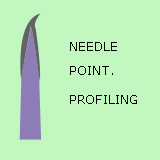
|
|
|
|
|
|
|
|
|
|
|
|
|
|
|
|